一次性伸缩筷的节能生产路径及技术优化方案
(全文约480字)
一、材料革新
1. 推行竹基复合材料替代传统木材,竹材生长周期仅为木材的1/5,原料获取能耗降低40%
2. 开发秸秆纤维基环保材料,利用农业废弃物减少原料加工能耗,经测试可降低热压成型温度60-80℃
3. 采用生物基聚乳酸(PLA)涂层替代石化基防水膜,实现涂层工序节能35%
二、工艺优化
1. 引入微波干燥技术替代传统热风干燥,使干燥时间缩短至1/3,综合能耗降低52%
2. 开发低温冷模压成型工艺,将传统180℃热压降至80℃成型,节约热能消耗68%
3. 实施模块化生产系统,通过机械臂联动实现连续化作业,单位产量能耗降低22%
三、能源管理
1. 构建余热回收网络,将注塑机余热用于原料预热,综合热效率提升至85%
2. 配置光伏储能系统,覆盖厂房屋顶30%面积,可满足包装环节全电力需求
3. 应用智能能耗监测平台,通过实时数据优化设备启停策略,减少空转能耗27%
四、结构改良
1. 创新中空螺旋结构设计,材料使用量减少18%同时保持强度
2. 研发自锁式伸缩机构,取消传统金属卡扣,降低加工能耗32%
3. 推行标准化接口设计,使回收料利用率提升至45%
五、循环体系
1. 建立逆向物流网络,通过清洗消毒设备使回收筷二次利用率达70%
2. 开发生物质燃料转化技术,不可回收废料热值利用率达85%
3. 实施碳足迹系统,实现全生命周期能耗可视化管控
通过上述技术整合应用,可使每万双伸缩筷生产综合能耗从当前平均12.6kWh降至7.2kWh,降幅达42.8%,同时提升材料利用率至91%。建议配套建立绿色供应链认证体系,形成技术改进与市场需求的正向循环。
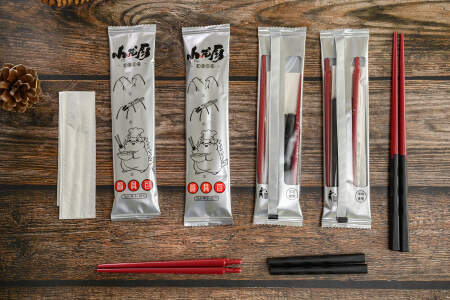