一次性伸缩筷的制造工艺可分为材料处理、结构成型、表面加工和消毒包装四个环节,需兼顾轻便性、耐用性与卫生安全要求。
1. 材料选择与预处理
主要采用竹木或食品级聚(PP塑料)。竹材需筛选5年以上竹龄的楠竹,经切割分片后蒸煮脱糖,60℃烘干至含水率8%-10%;塑料原料需通过FDA认证,采用注塑级颗粒料。两种材质均需通过重金属及微生物检测。
2. 精密结构制造
竹木型:数控机床加工三段式伸缩结构,上段内壁车削0.3mm深螺旋纹,中段外壁匹配0.28mm凸纹,公差控制在±0.02mm。塑料型:模具注塑成型带卡扣的伸缩套件,模具温度保持80℃,注射压力120MPa确保结构精密。连接部设计0.5mm缓冲间隙,提升伸缩顺滑度。
3. 表面精细化处理
竹筷经800目砂带三次抛光,微波灭菌后浸涂食用级;塑料件通过等离子处理增强表面附着力,再喷涂涂层(含0.5%纳米银)。末端设计防滑纹路,纹深0.1-0.15mm,纹距1mm。
4. 自动化装配与包装
机械臂完成三段式组装,扭矩传感器控制旋紧力度在0.15-0.2N·m。紫外线隧道(波长253.7nm)双重灭菌,残菌量≤50CFU/g。氮气置换包装,氧气含量<0.5%,延长保质期至18个月。
现代工艺采用模块化生产线,每分钟可产200-250双,良品率达99.3%。环保型产品开始使用PLA生物降解塑料,180天自然分解率达90%以上。关键控制点包括连接结构配合度、表面粗糙度(Ra≤0.8μm)和微生物指标,需通过AOAC检测认证。
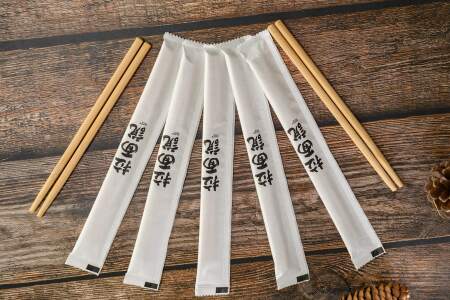